Fmea Software
APIS IQ Software page. Find info here on the free trial, product comparison, FMEA Software products, System requirements, Presentations and much more. Excerpt from PNSQC 2013 Proceedings PNSQC.ORG Copies may not be made or distributed for commercial use Page 1 Using FMEA to Improve Software.
For QFD, FMEA, Pugh, DFSS, or Six Sigma from. We have provided training to many Fortune 500 companies and can help yours as well. Seamless Integration into Excel 2000 or later Excel 2003 Integration (click to enlarge) Excel 2007 Integration (click to enlarge) FMEA Examples Create FMEA using SnapSheets XL is a snap. The wizard makes grouping functions, failure modes, and causes easy. SnapSheets XL Creates Blank Template Ready for you to edit (click to enlarge) Right anywhere in the worksheet to Add/Remove/Insert/Hide Columns or Pareto the results. (click to enlarge) Use 'Top 20 Pareto' to generate the top 20 causes sorted by RPN. (click to enlarge) For those that want more control over the pareto, create a Pareto just about anyway you want by using 'Custom Pareto'.
Sort by RPN, Severity, Occurrence, or Detection. Limits the number of items in the Pareto by absolute number or those which surpass a threshold.
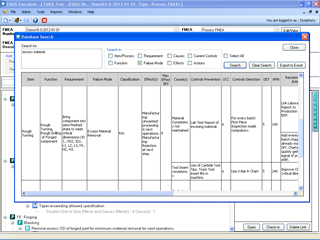
Generate the Pareto by Function, Failure Mode, or Cause. FMEA Worksheet (click to enlarge) Pugh Matrix (click to Enlarge) Larger House of Quality (click to enlarge) SnapSheets XL QFD Wizard (click to enlarge).
This article's may be too long for the length of the article. Please help by moving some material from it into the body of the article. Please read the and to ensure the section will still be inclusive of all essential details. Please discuss this issue on the article's. (January 2017) Failure mode and effects analysis ( FMEA)—also ' failure modes', plural, in most accurate publications—was one of the first highly structured, systematic techniques for. It was developed by in the late 1950s to study problems that might arise from malfunctions of military systems. An FMEA is often the first step of a system reliability study. Football Manager 2007 Full Crack.
It involves reviewing as many components, assemblies, and subsystems as possible to identify failure modes, and their causes and effects. For each component, the failure modes and their resulting effects on the rest of the system are recorded in a specific FMEA worksheet. There are numerous variations of such worksheets. An FMEA can be a qualitative analysis, but may be put on a quantitative basis when mathematical models are combined with a statistical failure mode ratio database. A few different types of FMEA analyses exist, such as: • Functional • Design • Process Sometimes FMEA is extended to (failure mode, effects, and criticality analysis) to indicate that criticality analysis is performed too. FMEA is an (forward logic) single point of failure analysis and is a core task in, and. Dj Virtual Pro 7 Full Con Crack. A successful FMEA activity helps identify potential failure modes based on experience with similar products and processes—or based on common physics of failure logic.
It is widely used in development and manufacturing industries in various phases of the product life cycle. Effects analysis refers to studying the consequences of those failures on different system levels. Functional analyses are needed as an input to determine correct failure modes, at all system levels, both for functional FMEA or Piece-Part (hardware) FMEA. Jaguar X Type Navigation Dvd. An FMEA is used to structure Mitigation for Risk reduction based on either failure (mode) effect severity reduction or based on lowering the probability of failure or both. The FMEA is in principle a full inductive (forward logic) analysis, however the failure probability can only be estimated or reduced by understanding the failure mechanism.
Ideally this probability shall be lowered to 'impossible to occur' by eliminating the. It is therefore important to include in the FMEA an appropriate depth of information on the causes of failure (deductive analysis). Contents • • • • • • • • • • • • • • • • • • • • • • Introduction [ ] The FME(C)A is a design tool used to systematically analyze postulated component failures and identify the resultant effects on system operations. The analysis is sometimes characterized as consisting of two sub-analyses, the first being the failure modes and effects analysis (FMEA), and the second, the criticality analysis (CA). Successful development of an FMEA requires that the analyst include all significant failure modes for each contributing element or part in the system. FMEAs can be performed at the system, subsystem, assembly, subassembly or part level. The should be a living document during development of a hardware design.
It should be scheduled and completed concurrently with the design. If completed in a timely manner, the FMECA can help guide design decisions. The usefulness of the FMECA as a design tool and in the decision-making process is dependent on the effectiveness and timeliness with which design problems are identified.